機械加工市場 サイズ - 分析
加工市場が評価されると推定される 米ドル 402.56 ベン に 2024 そして到達する予定 米ドル 625.55 によって 2031、混合の年次成長率で育つ 2024年から2031年にかけて6.5%のCAGR。 機械加工市場は、コンピュータ数値制御(CNC)機械の採用、マルチタスクマシンの需要増加、ハイブリッド加工プロセスの普及など、いくつかの重要な傾向を目撃しています。
調査期間 | 2024 - 2031 |
推定の基準年 | 2023 |
CAGR | 6.5% |
市場集中度 | High |
主要プレーヤー | ファナック株式会社, DMG森精機株式会社, 株式会社アマダ, アトラスコプコAB。, BystronicレーザーAG。 その他 |
*免責事項:主要プレーヤーは順不同で記載されています。
*出典:Coherent Market Insights
カスタマイズされたレポートを購入しますか?
お知らせください!
機械加工市場 トレンド
市場ドライバ - CNC技術によるオートメーションと統合の有利化
近年、加工業界が著しい技術の進歩を目撃しました。 コンピュータの数値制御(CNC)技術は、製造ワークフローにおける自動化と統合のより高いレベルを可能にしました。
特に自動車メーカーは、軽量車両設計に焦点を合わせ、燃料効率性を高めるため、CNC加工の採用が増加しています。 航空機のOEMはまた航空機エンジンおよび構造で使用される高度の合金そしてエキゾチックな材料を機械で造る機能のためのCNCを支持します。 医療機器メーカーは、小型インプラント部品の製造において、CNCを得意としています。
マシニング市場におけるもう一つの重要な傾向は、ロボティクス、3Dプリンティング、IoTセンサー、デジタルツインなどの他の技術を備えたCNCマシンの統合です。 この結果は、1台の機械のより速い変化および複数のプロセス機能の十分に自動化された適用範囲が広い製造業の細胞で。 このようなデジタルで接続された加工ハブは、金型の交換(SMED)などのリーン製造アプローチをサポートしています。 少量・多品種の商品ラインを最適化し、オンデマンド生産モデルを有効にすることで、加工市場における需要が高まります。
市場ドライバ - 自動車や航空宇宙などの産業における軽量で精密な加工の要求
業界全体の軽量設計に重点を置いたライジングは、高度な加工技術のための重要なドライバーです。 自動車空間では、自動車OEMおよびサプライヤーは、新材料選定と最適化されたコンポーネントエンジニアリングによる平均15〜20%の軽量化を追求しています。
エアロスペースは、加工能力をプッシュする別のヘビー級産業です。 飛行機メーカーは、ジェットエンジンやエアフレームのスーパーエンジニアリング合金と一緒に、カーボンファイバーなどのコンポジットを活用しています。 これらは、現代のエキゾチックな金属やコンポジットを最大限の精度で加工できる革新的な加工ソリューションを必要とします。 設計仕様からの逸脱でも、安全を防いでいただけます。
元の機器メーカー(OEM)と規制当局が厳しい締め切りを指摘し、機械加工市場は、ダイ(SMED)の1分の交換のようなリーン製造システムを急速に展開しています。 複数のプロセスを組み合わせるスマートな機械アプリケーションのためのこの呼び出しは、プラグアンドプロデュースクイックチェンジオーバー。 これらすべてのニーズは、機械ベンダーからの技術革新を燃料化し、この戦略的産業における継続的な成長見通しを運転しています。
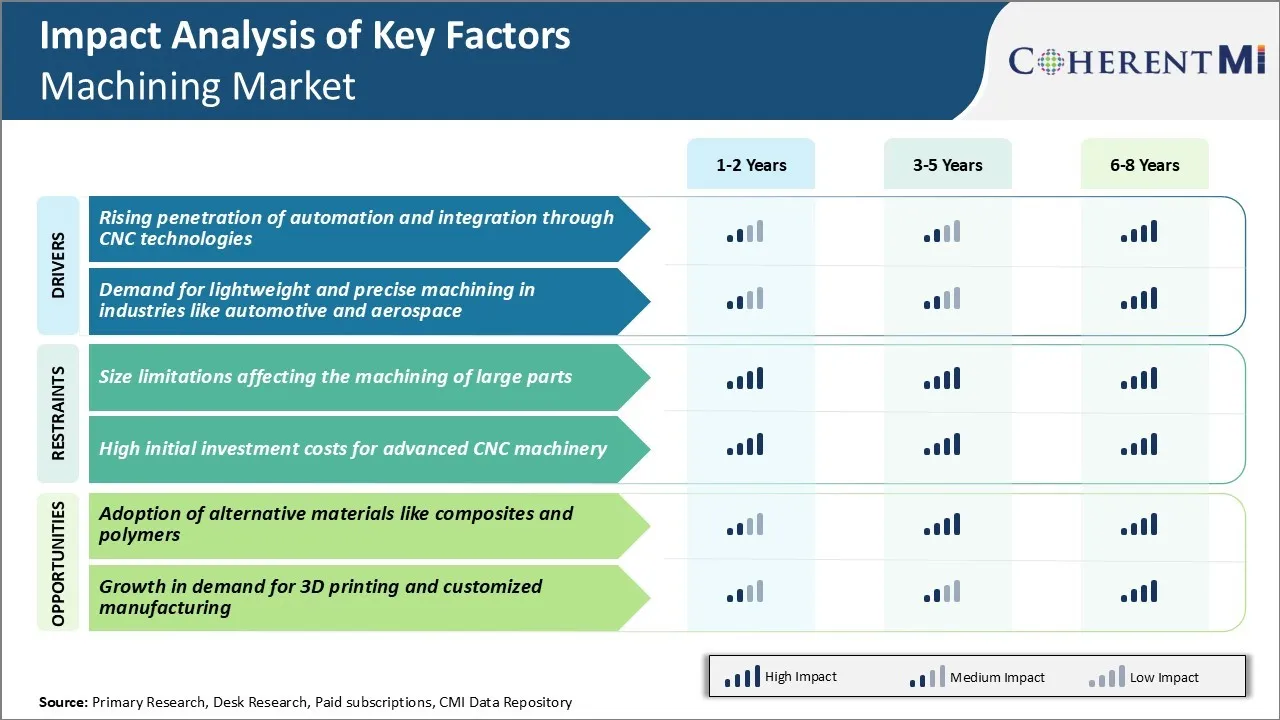
市場課題 - 大型部品の加工に影響を及ぼすサイズ制限
加工市場が直面する重要な課題の1つは、大きな部品を加工する場合のサイズ制限です。 従来のマシニング センターに機械で造ることができる部品の最大サイズを限る標準的な働く封筒があります。 航空宇宙、造船業、建設機械などの分野において、大きな複合材料や金属構造が一体化している。
航空機の胴体、船の船の船員または風力タービン ブレードを 1 枚で加工するには、余分な大きな作業量と高いペイロードの容量を持つ機械が必要です。 しかし、このような大型5軸マシニングセンタでは、大幅な資本投資や大型工場のフットプリントが必要となります。 また、高剛性・熱安定性に関するエンジニアリングの複雑性も拡大しています。
その結果、大きな部品は、多くの場合、アセンブリやサブアセンブリとして機械加工され、溶接または留め具を使用して一緒に結合する必要があります。 現在の加工技術の規模制約は、特定の業界において必要とされる大型モノリシック部品の製造のための高度です。
市場機会 - 複合材料やポリマーなどの代替材料の採用
加工市場にとって重要な機会は、高度な複合材料およびポリマー材料の採用の増加にあります。 軽量化はエネルギー効率および性能を改善することを目指している多くの企業セクターを渡る衝動になりました。 複合材料は、金属合金よりも同等の強度から重量比を上げる一方で、設計の創造的な自由を可能にします。 航空宇宙、自動車、船舶、再生可能エネルギー製品に採用が進んでいます。
繊維強化プラスチックとエンジニアリング熱可塑性の加工は、金属と比較して異なる課題を貫くだけでなく、市場を拡大する。 コンポジット製造が成長するにつれて、コンポジットコンポーネントの加工の必要性が大幅に上昇します。 特殊加工センターは、研磨水ジェット切断や高圧液ジェット侵食などの技術を用いてこれらの材料を扱うことができる開発されています。
層1サプライヤーからの高度なポリマー複合材の可用性は、加工の見通しも向上します。 代替材料のゲイン受容性として、加工市場は、関連する技術とプロセスを開発し、この傾向を増大する機会を持っています。
主要プレーヤーが採用した主な勝利戦略 機械加工市場
先端製造技術への投資: DMG Mori、Haas Automation、Doosan Machineなどの企業 ツールは、CNC機械、コンピュータ加工(CAM)ソフトウェア、および生産性と品質を向上させるための添加剤製造などの高度な技術に大きく投資しています。
カスタマイズされたソリューションに焦点を当てる: HardingeやJinan North Machinery Co.などのプレイヤーは、マシンを販売するだけでなく、顧客にカスタマイズされた柔軟な加工ソリューションを提供することに焦点を当てています。 適切な機械、工具細工、自動化、統合に関する顧客のプロセスや提案を理解しています。
戦略的買収: マシニング企業が他のプレイヤーを買収し、グローバルに展開しています。 たとえば、2021年にHurcoはインドのCNCルーターメーカーAkhuria CNCを買収し、インドの生産拠点を設立しました。 これにより、Hurco は成長するインド市場を直接提供するようになりました。
アフターマーケット営業とサービスに焦点を合わせる:小松や奥沼などの加工市場での主要選手が、アフターマーケットの売上の50%以上を稼いでいます。
セグメント分析 機械加工市場
洞察力、タイプによって:旋盤は精密工学能力を強調します
2024年の機械加工市場の35.3%のシェアのための旋盤機械の記述は、それらの多目的な性質および精密工学の機能が原因です。 旋盤機械の要求を運転する主要因は一貫性および均等性を必要とする大量生産の適用のためのそれらの適性です。 自動車や電子機器などの産業は、日常的に最小限の公差で、何千もの同じ部品を焼くために旋盤機に大きく依存しています。
別の主需要の運転者は企業を渡る複雑な機械化の必要性の上昇です。 旋盤機は、多軸コンピュータの数値制御システムと高度なツーリング機能により、このような幾何学的形態の精密加工を独自に実現します。
これらのセクターのメーカーは、旋盤機械に依存して、タイトな公差と複雑な切断パターンを図面ごとにプログラミングすることで、高度にカスタマイズされた部品の小さなバッチを生成します。 セットアップ変更なしで非標準部品要件に迅速に適応するこの能力は、旋盤機械が関連しています。
洞察、エンド使用による:自動車適用は大規模な機械化の容積と支配します
自動車産業は2024年に機械加工市場の40.2%のシェアを占めます。 これは、単一の車両で数千のコンポーネント部品を生成するために必要な巨大な加工量によるものです。 自動車加工の需要を燃料とする主要なドライバーは、毎年10億台に測定された自動車生産の規模です。 このような大規模な出力レベルを実現するため、超効率的な加工技術と生産システムが搭載され、高耐容性とボリュームで自動車部品をめぐり合わせることができます。
また、自動車製造プロセスの複雑さとカスタマイズニーズは、加工の柔軟性に優れています。 この高度に統合されたアプローチは、現代の自動車製造を定義する正式な生産方法とビルド・ツー・オーダーの大量生産モデルを達成するために不可欠です。
自動車環境内の密接で洗練された加工作業負荷を集中するこれらの要因の混乱は、世界的な加工技術のための最大のエンドユーザー産業としての地位を隠しました。
追加の洞察 機械加工市場
- 産業オートメーションのCNC機械の上昇の使用は機械化の市場の成長を後押しします。
- 精密な部品製造の要求によるCNC旋盤機械の成長は機械化の市場の上昇傾向です。
- アジア・パシフィックは、費用対効果の高い操作と原材料の可用性により、加工市場を支配します。 しかし、欧州はドイツ、フランス、イタリアが主導し、著しく成長する予定です。
競合の概要 機械加工市場
マシニング市場で動作する主要な選手は、株式会社ファンック、DMG MORI、株式会社アマダ、アトラスコプコAB、Bystronic Laser AG、TRUMPF GmbH、株式会社オクマ、サンドビックAB、ヤマザキマザック、IPGフォトニクス株式会社などがあります。
機械加工市場 リーダー
- ファナック株式会社
- DMG森精機株式会社
- 株式会社アマダ
- アトラスコプコAB。
- BystronicレーザーAG。
*免責事項:主要プレーヤーは順不同で記載されています。
機械加工市場 - 競合関係
市場が分散
(多くのプレーヤーが参入し、競争が激しい。)
*出典:Coherent Market Insights最近の動向 機械加工市場
- 2023年2月、雇用主とCNCの町家をつなぐ専門職のHireCNCが誕生しました。 プラットフォームは、米国およびカナダ市場でのCNC関連ジョブに焦点を当て、CNC加工業界の求職者と雇用者の両方の雇用プロセスを合理化することを目指しています。
- 2023年1月、三菱電機インドのCNC事業部が「Teach-T」を導入し、学生のCNC技術教育を強化 この取り組みは、政府の入札やプロジェクト、ITIs、卒業証書コース、民間工学のトレーニングセンターなど、教育分野に参入するための企業戦略と整合しています。
- 三菱電機インディアは、製造の効率化と技術革新を目指し、CNCのM800VとM80Vシリーズを導入しました。 これらのCNCは、業界初のビルトイン無線LANを備え、リモートアクセスと制御を可能にし、ポストパンデミック時代に特に有益です。
機械加工市場 レポート - 目次
- OBJECTIVESとASSUMPTIONSを探す
- マーケットプレイス
- レポートの説明
- エグゼクティブ・サマリー
- 機械化の市場, タイプ別
- エンド使用による機械化の市場
- コヒーレントの機会マップ (COM)
- マーケットダイナミクス、地域、トレンド分析
- マーケット・ダイナミクス
- 衝撃解析
- 主なハイライト
- 規制シナリオ
- プロダクト進水/承認
- PEST分析
- PORTERの分析
- 合併・買収シナリオ
- 世界の機械化の市場、タイプによって、2024-2031、(USD Bn)
- 導入事例
- 市場シェア分析、2024年、2031年
- Y-o-Y成長分析、2019 - 2031
- セグメントトレンド
- 旋盤機械
- 導入事例
- 市場規模と予測、Y-o-Y成長、2019-2031、(USD Bn)
- レーザー加工機
- 導入事例
- 市場規模と予測、Y-o-Y成長、2019-2031、(USD Bn)
- フライス盤
- 導入事例
- 市場規模と予測、Y-o-Y成長、2019-2031、(USD Bn)
- 粉砕機
- 導入事例
- 市場規模と予測、Y-o-Y成長、2019-2031、(USD Bn)
- ウィンド マシーン
- 導入事例
- 市場規模と予測、Y-o-Y成長、2019-2031、(USD Bn)
- 溶接機
- 導入事例
- 市場規模と予測、Y-o-Y成長、2019-2031、(USD Bn)
- 世界の機械化の市場, エンドユース、2024-2031、(USD Bn)
- 導入事例
- 市場シェア分析、2024年、2031年
- Y-o-Y成長分析、2019 - 2031
- セグメントトレンド
- 自動車産業
- 導入事例
- 市場規模と予測、Y-o-Y成長、2019-2031、(USD Bn)
- 航空宇宙・防衛
- 導入事例
- 市場規模と予測、Y-o-Y成長、2019-2031、(USD Bn)
- 建設機械
- 導入事例
- 市場規模と予測、Y-o-Y成長、2019-2031、(USD Bn)
- 電力とエネルギー
- 導入事例
- 市場規模と予測、Y-o-Y成長、2019-2031、(USD Bn)
- 産業
- 導入事例
- 市場規模と予測、Y-o-Y成長、2019-2031、(USD Bn)
- グローバルマシニング市場, 地域別, 2019 - 2031, 値 (USD Bn)
- 導入事例
- 市場シェア(%) 分析, 2024,2027 & 2031, 値 (USD Bn)
- 市場Y-o-Y成長分析 (%)、2019 - 2031、値(USD Bn)
- 地域動向
- 北アメリカ
- 導入事例
- 市場規模と予測, タイプ別, 2019 - 2031, 値 (USD Bn)
- 市場規模と予測, エンド使用, 2019 - 2031, 値 (USD Bn)
- ラテンアメリカ
- 導入事例
- 市場規模と予測, タイプ別, 2019 - 2031, 値 (USD Bn)
- 市場規模と予測, エンド使用, 2019 - 2031, 値 (USD Bn)
- ヨーロッパ
- 導入事例
- 市場規模と予測, タイプ別, 2019 - 2031, 値 (USD Bn)
- 市場規模と予測, エンド使用, 2019 - 2031, 値 (USD Bn)
- ドイツ
- アメリカ
- スペイン
- フランス
- イタリア
- ロシア
- ヨーロッパの残り
- アジアパシフィック
- 導入事例
- 市場規模と予測, タイプ別, 2019 - 2031, 値 (USD Bn)
- 市場規模と予測, エンド使用, 2019 - 2031, 値 (USD Bn)
- 中国・中国
- インド
- ジャパンジャパン
- オーストラリア
- 韓国
- アセアン
- アジアパシフィック
- 中東
- 導入事例
- 市場規模と予測, タイプ別, 2019 - 2031, 値 (USD Bn)
- 市場規模と予測, エンド使用, 2019 - 2031, 値 (USD Bn)
- アフリカ
- 導入事例
- 市場規模と予測, タイプ別, 2019 - 2031, 値 (USD Bn)
- 市場規模と予測, エンド使用, 2019 - 2031, 値 (USD Bn)
- 競争力のある土地
- ファナック株式会社
- 企業ハイライト
- 製品ポートフォリオ
- 主な開発
- 財務・業績
- 戦略
- DMG森精機株式会社
- 企業ハイライト
- 製品ポートフォリオ
- 主な開発
- 財務・業績
- 戦略
- 株式会社アマダ
- 企業ハイライト
- 製品ポートフォリオ
- 主な開発
- 財務・業績
- 戦略
- アトラスコプコAB。
- 企業ハイライト
- 製品ポートフォリオ
- 主な開発
- 財務・業績
- 戦略
- BystronicレーザーAG。
- 企業ハイライト
- 製品ポートフォリオ
- 主な開発
- 財務・業績
- 戦略
- TRUMPF GmbH Co., Ltd. 代表取締役 兼社長
- 企業ハイライト
- 製品ポートフォリオ
- 主な開発
- 財務・業績
- 戦略
- オクマ株式会社
- 企業ハイライト
- 製品ポートフォリオ
- 主な開発
- 財務・業績
- 戦略
- サンドビックAB.
- 企業ハイライト
- 製品ポートフォリオ
- 主な開発
- 財務・業績
- 戦略
- 山崎マザック株式会社
- 企業ハイライト
- 製品ポートフォリオ
- 主な開発
- 財務・業績
- 戦略
- IPGフォトニクス株式会社
- 企業ハイライト
- 製品ポートフォリオ
- 主な開発
- 財務・業績
- 戦略
- アナリストの提言
- フォーチュンホイール
- アナリストビュー
- コヒーレントの機会マップ
- 参考文献と研究方法論
機械加工市場 セグメンテーション
- タイプ別
- 旋盤機械
- レーザー加工機
- フライス盤
- 粉砕機
- ウィンド マシーン
- 溶接機
- エンド使用
- 自動車産業
- 航空宇宙・防衛
- 建設機械
- 電力とエネルギー
- 産業
購入オプションを検討しますか?このレポートの個々のセクション?
About authorRamprasad Bhute は、市場調査とビジネスコンサルティングで 6 年以上の経験を持つシニアリサーチコンサルタントです。建設工学と産業オートメーションおよび機械を専門とするこの専門家は、プロセスの最適化と運用効率の向上に特化した強力なスキルセットを開発しました。注目すべき業績には、大幅なコスト削減と生産性の向上をもたらした重要なプロジェクトを主導したことなどがあります。たとえば、彼は大手建設会社の機械プロセスの自動化で重要な役割を果たし、運用効率を 25% 向上させました。複雑なデータを分析し、実用的な洞察を提供する能力により、彼はこの分野で信頼できるアドバイザーとなっています。
よくある質問 :
加工市場は2024年のUSD 402.56 Bnで評価され、2031までにUSD 625.55 Bnに達すると予想されます。
高度なCNC機械のための大きな部品と高い初期投資コストの加工に影響を与えるサイズの制限は、加工市場の成長を妨げる主要な要因です。
CNC技術による自動化と統合の普及と自動車や航空宇宙などの産業における軽量かつ精密な加工の要求は、加工市場を牽引する主要な要因です。
株式会社ファンヌック、株式会社DMG森、株式会社アマダ、アトラスコプコAB、Bystronic Laser AG、TRUMPF GmbH Co.、株式会社オクマ、サンドビックAB、山崎マザック、IPGフォトニクスは、主要な選手です。
加工市場のCAGRは、2024-2031から6.5%となるように計画されています。